Prototyping Manufacturing Glossary: CNC Machining, 3D Printing,Sheet Metal Fabrication,
Injection molding
There's a lot of industry terms to sort through in manufacturing. Explore our glossary for quick definitions of
frequently used manufacturing terms and acronyms.
~
2.5 Axis or 2.5D CNC
2.5D refers to a machining scenario in which there are no overhanging elements to the part. In other words, everything that must be reached can be reached by plunging straight down from above.
3 Axis or 3D CNC
Refers to a machine or CNC scenario that has 3 axes of motion available, usually X, Y, and Z.
3DM (see also "Rhino")
3DM is the file extension for a Rhino 3D CAD file.
4 Axis CNC
Refers to a scenario or machine in which 4-axes of motion are available. Usually these are X, Y, Z, and a 4th rotational axis. The 4th axis is typically the ability to rotate along an axis normally parallel to the X-axis, and is usually referred to as the “A” axis.
This capability is extremely useful for a lot of situations. For example, it allows machining features onto a curved surface, such as a shaft or cylinder, as the shaft or cylinder is rotated in the 4th axis. It can also allow access to the underside of a part or direct access to the sides without having to manually flip the part to another orientation.
5 Axis CNC adds a second rotational axis to the X, Y, Z, and A axes for even greater flexibility.
Programming a 4 axis system can be more complex, and a 5 axis system is extremely complex to program.
See also "Axes", “4th Axis” and “5 Axis CNC”.
4th Axis
The term “4th Axis” often refers to the hardware necessary to add a 4th axis to a 3 axis CNC machine. This hardware typically consists of a motorized rotary table mounted on the machines table and aligned so its axis is congruent with the x-axis of the machine.
5 Axis CNC
5-Axis CNC is generally a mill or router that has an X, Y, and Z-axis working perpendicular to one another together with two rotating axes. Imagine a 4th axis rotating table that is used to rotate a 5th axis that can also rotate at right angles to the 4th axis.
This configuration provides the maximum machining flexibility in a single setup of any of the CNC configurations. Certain types of applications almost require 5-axis machining to be successful. For example, cylinder head porting requires the milling cutter to reach inside a convoluted intake or exhaust port in a cylinder head, a task that would be just about impossible to do in more conventional configurations.
5-axis machines are generally quite expensive and difficult to program, however. See also "Axes" for a diagram of the 5 different axes.
5-axes are required for a general purpose CNC tool grinder/sharpener, and you can see why if you examine the geometry involved:
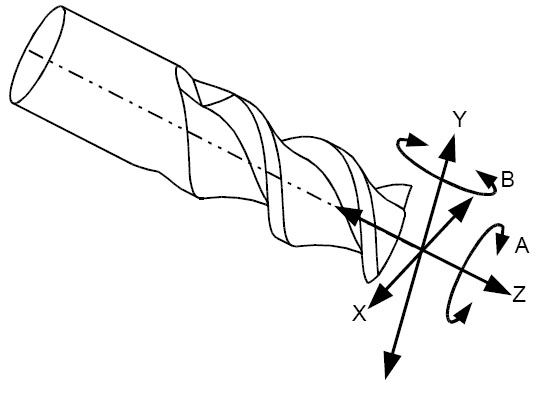
5-axes needed for Tool Grinding...
The "A" axis is used to access the cutter around its circumference. The "B" axis is needed for cutters such as ball mills that are not just cylindrical the whole length of the tool.
5-Axis machines may be characterized as "continuous" (also called "simultaneous") or "positional" (sometimes called "indexing"). A 5-axis continuous machine is capable of cutting while all 5 axes move. This allows continuous machining over complex shapes, and is more powerful than 5-axis positional. A positional machine can only cut in 3 axes at a time, but it can position before cutting using all 5 axes. The positional approach is much simpler to implement, both for software and hardware, and so may be found in older or lower end machines. 5-axis positional or indexed is also sometimes called 3+2 axis.
In theory, you can cut any part with 5-axis positional that you could cut with 5-axis continuous. A machine designed for continuous should be faster. In addition, 5-axis positional may introduce dwells (See also dwell) that result in visible marks in the surface finish.
A
A-Axis
The A-Axis is the rotational axis about the X-Axis.
ABEC
ABEC is the abbreviation for Annular Bearing Engineering Council. It is a term commonly used in conjunction with rating bearing tolerances or precision. A number follows the ABEC designation, and the higher the number, the more precise the bearing. An ABEC 7 bearing is an excellent machine tool grade bearing.
The ABEC system relates to other bearing precision rating systems as follows:
ABEC SYSTEM
|
|
ISO SYSTEM
|
|
DIN SYSTEM
|
ABEC 1
|
|
Normal
|
|
P0
|
ABEC 3
|
|
Class 6
|
|
P6
|
ABEC 5
|
|
Class 5
|
|
P5
|
ABEC 7
|
|
Class 4
|
|
P4
|
ABEC 9
|
|
Class 2
|
|
P2
|
Absolute Coordinates
Absolute coordinates are expressed relative to a fixed position whereas Relative Coordinates (see also) are relative to the current position of the cutting tool. The G90 command places the part program into absolute coordinate mode. G91 cancels absolute coordinate mode and places the part program into relative coordinate mode.
Absolute Move
An absolute move is made using absolute coordinates, so it commands motion to an exact location specified relative to the origin of the coordinate system. A relative move is made using relative coordinates and so is specified as a move from the current position
Accuracy
Accuracy is the difference between the expected value and the actual value of some measurement.
Acetal
When combined with PTFE (Teflon), acetal makes an excellent low friction material with which to coat machine ways. This is the material used on the Tormach CNC mill, for example. Rulon and Turcite are all trade names for the PTFE + Acetal combination. Delrin is the trade name for pure Acetal. See Also Delrin.
ACME Screw
ACME is the most common type of leadscrew found in machine tool applications. The ACME thread is a particular type of thread. Compared to a ballscrew (see also Ballscrew), ACME leadscrews have very high friction and backlash, both of which are undesirable attributes for high performance CNC applications.
On the other hand, ACME leadscrews can be made to very high precision, and they are often cheaper than ballscrews. They are almost universally the choice for manual machines.
Active High/Low Logic
The terms "Active High" and "Active Low" refer to how electrical signals are interpreted. In Active High logic, the presence of a higher voltage (within a specified range) indicates a signal is present. Active High logic is also referred to as "Open Collector" logic. While it may seem odd to use the absence of voltage to indicate the presence of a signal, there are advantages to this approach. In general, it gives the circuit a much broader tolerance for the voltages used.
In Active Low logic, a ground or low voltage (within a specified range) indicates a signal is present.
Additive manufacturing, 3D printing
Commonly used interchangably, additive manufacturing (3D printing) involves a CAD model or scan of an object that is reproduced, layer by layer, as a physical three-dimensional object. Stereolithography, selective laser sintering, fused deposition modeling and direct metal laser sintering are some of the commonly employed additive processes.
Angular Contact Bearing
Angular Contact Bearings are ball bearings designed to deal with heavier axial loads. A typical ball bearing is designed to deal with pure radial loads and are not well supported the closer the load comes to the axis of the bearing. They are commonly used to support leadscrews and in building precision spindles for machine tools.
There is a complex system of standardized nomenclature used to identify the characteristics of an AC Bearing from the part number. For example, AC Bearings have a contact angle that determines how far off axis they are supported for loads, they have a precision (See also ABEC), the have preload specifications (See also Preload), they have dimensional characteristics in terms of their bore, outer diameter, etc., and they have ratings that relate to their maximum operating speeds in RPM.
The best place to learn more about angular contact bearings is from the manufacturer's bearing catalogs:
Barden Timken NSK FAG
Annealing
Annealing is a heat treating process that is designed to remove the hardness of a material so that it can be machined.
Arbor
An arbor can be either a workholding device, or a toolholder. As a workholder, it generally refers to a device that can expand it's OD to clamp the ID of a workpiece. As a toolholder, it is similar to a spindle and is used in conjunction with grinding and buffing. A very similar term is "Mandrel".
Anodized (Type II Or Type III)
Type II (MIL-A-8625, Type II) creates a corrosion-resistant finish. Parts can be anodized in different colors—clear, black, red, and gold are most common—and is usually associated with aluminum. Type III (MIL-A-8625, Type III, Class 1/2 'hardcoat') is thicker and creates a wear-resistant layer in addition to the corrosion resistance seen with Type II.
ASE
ASE is the file extension for 3DS Max ASCII export files from Autodesk. In other words, a CAD file.
ATC: Automatic Tool Changer
Accuracy is the difference between the expected value and the actual value of some measurement.
Automatic Grinding Center
A CNC machining center that does grinding. Most automatic grinding centers are used to grind and sharpen tools and inserts.
See also Machining Center.
A-Side
Sometimes called the “cavity,” it is the half of the mold that usually creates the exterior of a cosmetic part. The A-side usually does not have moving parts built into it.
Axes
Following are diagrams depicting the basic axes for mills and lathes:
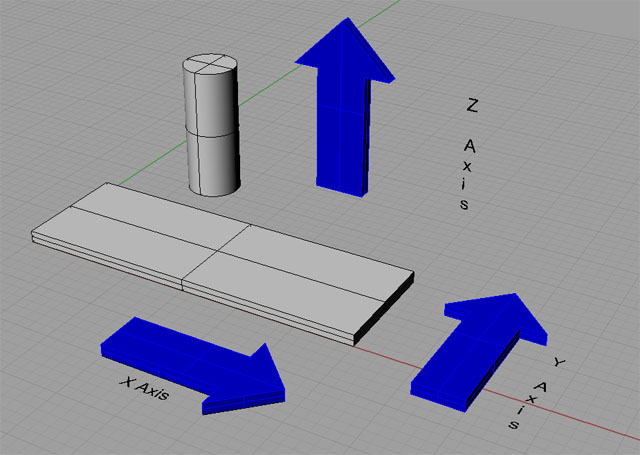
Mill Axes
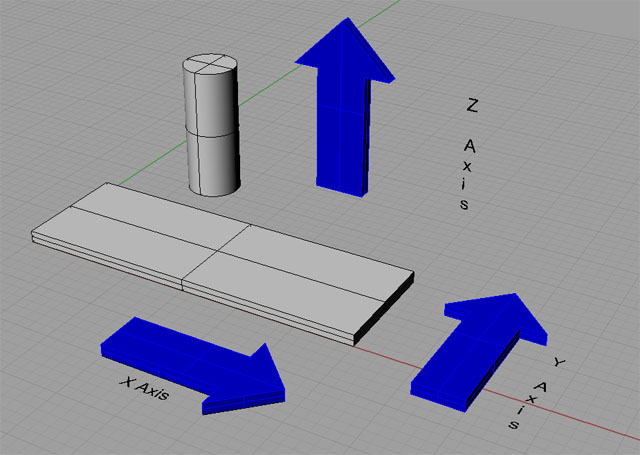
Lathe Axes
On a 4-axis or 5-axis mill there are additional rotational axes. Here is an example of a 5-axis mill with trunion table:
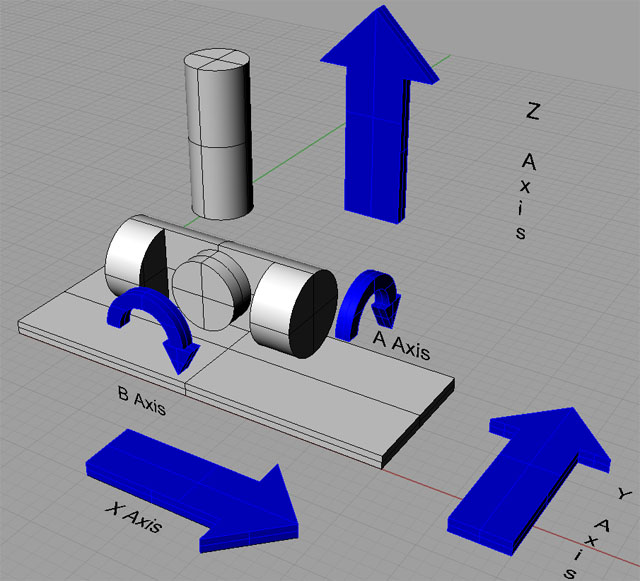
A 4-Axis Mill simply omits the B-Axis.
Axial hole
This is a hole that is parallel to the axis of revolution of a turned part, but does not need to be concentric to it.
B
Barrel
A component of the injection-molding machine wherein the resin pellets are melted, compressed and injected into the mold’s runner system.
Bead Blast
The part surface is left with a smooth, matte appearance.
Black oxide
Black oxide is a conversion coating used to improve corrosion resistance and minimize light reflection.
Bevel
Also known as a “chamfer,” it is a flat truncated corner.
Boss
A raised stud feature that is used to engage fasteners or support features of other parts passing through them.
Bridge tool
A temporary or interim mold made for the purpose of making production parts until a high-volume production mold is ready.
Brushed
Brushing is a surface treatment process in which abrasive belts are used to draw traces on the surface of a material, usually for aesthetic purposes. The thickness of the abrasive belts (usually between \#80-120) affects the finish. Although suitable for a handful of metals, brushing is most commonly applied to aluminum.
B-side
Sometimes called the “core,” it is the half of the mold where ejectors, side-action cams and other complex components are located. On a cosmetic part, the B-side usually creates the inside of the part.
Build platform
The support base on an additive machine where parts are built. The maximum build size of a part is dependent on the size of a machine’s build platform. Many times a build platform will house a number of different parts of varying geometries.
Bumpoff
A feature in the mold with an undercut. To eject the part, it must bend or stretch around the undercut.
C
CAD (Computer Aided Design or Drafting)
CAD programs are basically drawing programs used to create a plan or drawing of a part. There are a lot of different CAD programs. Some of the most popular include Autodesk, Rhino3D (See Also Rhino3D), and Solidworks.
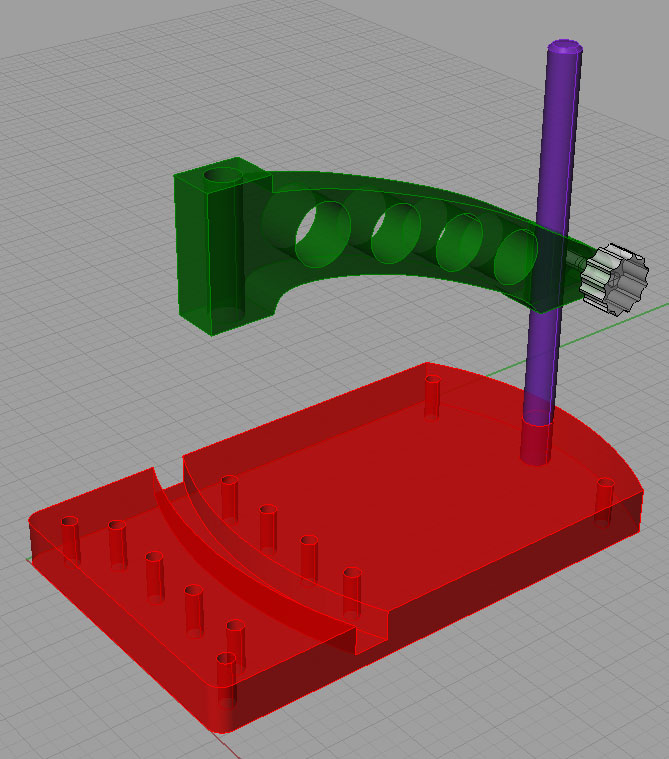
CAD Drawing of a Bench Tapper Made in Rhino 3D...
CAM (Computer Aided Manufacturing)
CAM is software that can generate G-Codes from a drawing. Often it is an add-on module for whatever CAD program you or using (VisualMill for Rhino3D is an example), or perhaps the CAM program incorporates its own CAD capability (OneCNC would be an example).
CAM programs make it much easier to generate complex G-Code part programs automatically, rather than having to write the codes by hand. There are many specialized CAM programs as well, such as programs that may be used to generate G-Codes that produce a router carving based on a bitmap (VCarve is an example).
Cavity
The void between the A-side and B-side that is filled to create the injection-molded part. The A-side of the mold is also sometimes called the cavity.
Cartesian Coordinates
Named for mathematician René Descartes, Cartesian coordinates provide a system for identifying the relative locations of points in space. Locations are specified by a set of numbers, with one number for each dimension (or axis if you are thinking CNC, See Also Axes). Each dimension is orthogonal to the others, meaning it is at right angles. Dimensions are usually lettered from X to Z for three dimensional. The number specifies how far from the Origin (See Also Origin) to travel along a particular dimension. The sign of the value determines which direction to travel from the origin.
C-Axis
The C-Axis is the rotational axis about the Z-Axis.
Center Cutting
A center cutting end mill is one that has the ability to cut with the center of it’s bottom face. This is crucial if you intend to plunge the end mill, which is to send it straight down the way you would a drill bit. Some end mills are not centercutting, and the cannot plunge straight down as a result. Often, a larger non center cutting end mill is not center cutting because there is a coolant passage down the core of the tool that allows coolant to be injected directly into the cutting action instead of coming from above.
Chamfer
A chamfer is beveling applied to an edge so it will not be sharp. This can be done for reasons of appearance and feel, or to avoid weakness for stress. For two surfaces that meet at right angles, imagine a chamfer at a 60 or 45 degree angles that just takes the edge off for a very short distance. Chamfering is a common machining operation, and it can also be useful as a means of deburring sharp edges.
There are tools specially made for chamfering, especially chamfering holes. I like Zeo's zero flute chamfering tools for holes.
Clamp force
The force required to hold the mold shut so resin cannot escape during injection. Measured in tons, as in “we have a 700 ton press.”
Counterbore
Counterboring is a common machining operation. It is often used to recess a bolt head down into the hole. The are counterbore cutters specifically made for the task, or some folks plunge cut with endmills. The endmill will not leave quite as flat a hole as a true counterbore, but it is often good enough.
Contoured pins
Ejector pins with the ends shaped to match a sloping surface on the part.
Core
A portion of the mold that goes inside a cavity to form the interior of a hollow part. Cores are normally found on the B-side of a mold, thus, the B-side is sometimes called the core.
Core pin
A fixed element in the mold that creates a void in the part. It is often easier to machine a core pin as a separate element and add it to the A-side or B-side as needed. Steel core pins are sometimes used in aluminum molds to create tall, thin cores that might be too fragile if machined out of the bulk aluminum of the mold.
Core-cavity
A term used to describe a mold created by mating A-side and B-side mold halves.
Cycle time
The time it takes to make one part including the closing of the mold, the injection of the resin, the solidification of the part, the opening of the mold and the ejection of the part.
D
Deflection
Deflection is unintended bending of a tool, workpiece, or machine component. It leads to inaccuracy or perhaps worse if it causes damage to the tool, workpiece, or machine. Rigidity is the counter to deflection.
Detent Torque
This is the torque you feel when you twist a stepper motor that has no power applied to it. The detent torque can cause a stepper motor to try to hold its position even when power is switched off, at least to the nearest step. With no power, the microstep position will be lost.
Direct metal laser sintering (DMLS)
DMLS employs a fiber laser system that draws onto a surface of atomized metal powder, welding the powder into a solid. After each layer, a blade adds a fresh layer of powder and repeats the process until a final metal part is formed.
Direction of pull
The direction the mold surfaces move when they are moving away from the part surfaces, either when the mold opens or when the part ejects.
Draft
A taper applied to the faces of the part that prevent them from being parallel to the motion of the mold opening. This keeps the part from being damaged due to the scraping as the part is ejected out of the mold.
Drying of plastics
Many plastics absorb water and must be dried prior to injection molding to ensure good cosmetics and material characteristics.
Durometer
A measure of a material's hardness. It is measured on a numeric scale ranging from lower (softer) to higher (harder).
DOC (Depth of Cut)
Depth of cut is a measurement of how much material the cutter is removing along one axis. So, a ½” endmill whose end is 0.020” into the surface of the material being cut, either below the face in the Z-direction or along the sides of a slot or pocket in the X or Y directions, has a 0.020” depth of cut.
Obviously it takes more power to run a higher depth of cut. You may need to run at a slower feed rate or spindle speed if you run a greater depth of cut. For CNC machines, it can be more advantageous to reduce the depth of cut, increase spindle and feed rates, and just make more passes to reach the desired depth.
Depth of cut is typically less than the diameter of the cutter, and sometimes much less depending on the rigidity of the machine and cutter.
Dongle
Dongles, also called USB Keys, are electronic keys that are used to copy protect software such as CAD or CAM software. The software will not operate unless the dongle is in place on the machine trying to run the software.
DWG File
An AutoCad CAD file format.
DXF File
A portion of the mold that goes inside a cavity to form the interior of a hollow part. Cores are normally found on the B-side of a mold, thus, the B-side is sometimes called the core.
E
Edge Finder
A device used to find the exact edge of the workpiece along the x or y axis. Edge finders can rely on electrical contact, a sensitive pressure switch, or be strictly mechanical.
Edge gate
An opening aligned with the parting line of the mold where resin flows into the cavity. Edge gates are typically placed on an outside edge of the part.
EDM
Electric discharge machining. A moldmaking method which can create taller, thinner ribs than milling, text on top of ribs and square outside edges on parts.
Ejection
The final stage of the injection-molding process where the completed part is pushed from the mold using pins or other mechanisms.
Ejector pins
Pins installed in the B-side of the mold that push the part out of the mold when the part has cooled sufficiently.
Elongation at break
How much the material can stretch or deform before breaking. This property of LSR allows for some difficult parts to be surprisingly removed from molds. For example, LR 3003/50 has an elongation at break of 480 percent.
End Mill or Endmill
End mills are cutters used in milling machines. They superficially resemble drill bits, although it is very superficial. There are a number of characteristics involved in selecting the best endmill for the job including:
- Number of flutes. Endmills may be had in a variety of configurations including 2, 3, 4, or more flutes.
- Roughing or Finish Style: Roughing endmills are good for hogging out material, but not so great for finishing.
- Centercutting: Determines whether the endmills center cuts. If not, the mill cannot be used to plunge cut. See Also Centercutting.
- Material: Endmills are made from a variety of materials ranging from High Speed Steel to Solid Carbide.
- Coating: There are a variety of coatings designed to improve the performance of the endmill.
- Type: Standard, ball nose, double ended, etc.
- Length: Shorter endmills are more rigid (See also Rigidity), longer endmills may be needed to reach.
- Diameter
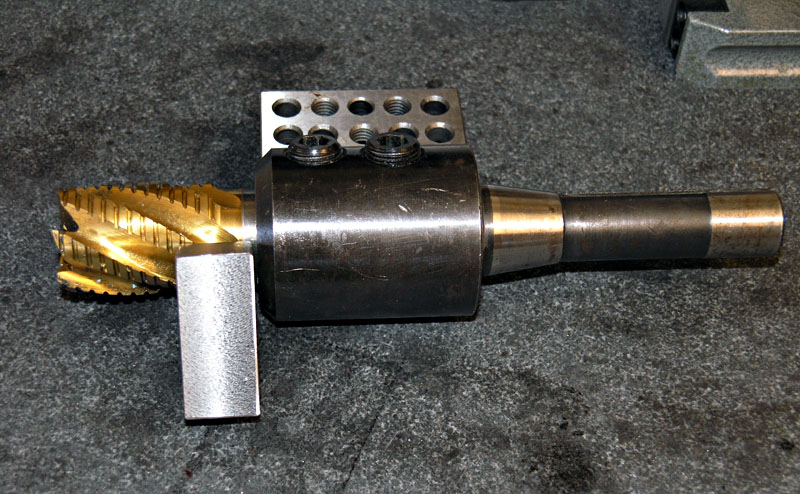
Roughing Endmill in an R8 Shank Millholder...
ESD
Electro static discharge. An electrical effect that may necessitate shielding in some applications. Some special grades of plastic are electrically conductive or dissipative and help prevent ESD.
F
Face Mill or Facemill
Face milling is the act of milling a surface perpendicular to the axis of rotation of the cutter. A face mill is a cutter specifically designed for this purpose.
Family mold
A mold where more than one cavity is cut into the mold to allow for multiple parts made of the same material to be formed in one cycle. Typically, each cavity forms a different part number. See also “multi-cavity mold.”
Fillet
A curved face where a rib meets a wall, intended to improve the flow of material and eliminate mechanical stress concentrations on the finished part.
Finish
A specific type of surface treatment applied to some or all faces of the part. This treatment can range from a smooth, polished finish to a highly contoured pattern that can obscure surface imperfections and create a better looking or better feeling part.
Flame retardant
A resin formulated to resist burning
Flash
Resin that leaks into a fine gap in the parting lines of the mold to create an undesired thin layer of plastic or liquid silicone rubber.
Flow marks
Visible indications on the finished part that show the flow of plastic within the mold prior to solidification.
Follow Turning
In follow turning two tools and two independent tool turrets are used on a CNC lathe to speed cutting. Each tool cuts at the desired depth of cut, with the second tool starting its cut where the first left off. In this way, twice as much material can be removed per pass.
Food grade
Resins or mold release spray that are approved for use in the manufacture of parts that will contact food in their application.
Fused deposition modeling (FDM)
Fused Deposition Modeling (FDM) is a 3D printing technology widely known for its speed, accuracy, and competitive cost. An FDM machine precisely extrudes melted plastic filament to create a part.
G
G12/G13 Circular Pocket Milling
G12 and G13 are G-Codes (see also G-Codes) in the part program that specify a circular pocket be milled. G12 causes the pocket to be milled in a clockwise direction while G13 mills counterclockwise. The radius of the circle is typically specified with an "I" command. For example "G12I5" specifies a pocket with a radius of 5 be cut in the clockwise direction. The cutter should be positioned to the center of the circular pocket using a move in a prior block or an X and Y command in the same block. The tool will return to center when the pocket is finished.
Clockwise and counterclockwise variants are provided so that the user may select climb versus conventional (see also Climb Milling and Conventional Milling). For example, with clockwise spindle rotation, G12 (clockwise) results in conventional milling.
Note that with a suitable cutter, such as a woodruff key cutter (see also Woodruff Cutter), it is possible to use G12/G13 to cut grooves or slots in the pocket wall.
Circular pocket milling is how CNC'ers cut holes larger than their cutter. It is sometimes called spiral interpolation and sometimes helical interpolation. True helical interpolation involves a helix, while spiral interpolation keeps the entire cut in the same plane.
Gantry Mill
A gantry mill uses a bridge-like arrangement to support the Z-Axis, which travels across the bridge for Y-Axis motion. They are very common for router and plasma applications, and somewhat less so except for large configurations when milling steel.
Gate
The generic term for the portion of the mold where resin enters the mold cavity.
GF
Glass-filled. This refers to a resin with glass fibers mixed into it. Glass-filled resins are much stronger and more rigid than the corresponding unfilled resin, but are also more brittle.
Gusset
A triangular rib that reinforces areas such as a wall to a floor or a boss to a floor.
H
Hot tip gate
A specialized gate that injects the resin into a face on the A-side of the mold. This type of gate doesn’t require a runner or sprue.
Handwheels
Handwheels are used to manually operate the axis of a CNC machine. They are generally connected to an electronic device called an MPG (See Also MPG) that sends signals through the CNC controller to the drive motors rather than directly moving the machinery via a leadscrew.
Hardness
Hardness is a material's resistance to plastic deformation and scratching. It is a measure of how difficult it is for the cutting tool to cut the material. Knowing the hardness of a material is helpful in deciding how to go about machining it, particularly for materials like steel where there are many different alloys and heat treatments (See Also Heat Treatment) that lead to a wide range of hardnesses.
There are a variety of scales used to measure hardness, including Rockwell, Brinell, Vickers, and Knoop. Testers are also available that can determine the hardness of a material in various ways. If you know what allow you are using, Machinery's Handbook and other reference sources will have hardness information.
Harmonic Drive
A harmonic drive is a gear drive of novel design that offers minimal backlash. As such they are ideal reduction drives to go between stepper or servo motors and the machine axis.
Heat Treatment
Heat Treatment is the process of using heat in very controlled ways to change the properties of a material. For example, heat treatment may be used to harden certain alloys of steel.
Helical Beam Coupler
A type of shaft coupler that has a helical slot cut through the middle. This allows the coupler to flex which enables coupling of shafts that are not quite true to one another. Helical Beam Couplers are a popular way to couple stepper and servo shafts to the reduction drive.
Helical Interpolation
A coordinated motion in x, y, and z axes that causes the tool to follow a helix. Helical interpolation is useful for a variety of operations, including ramping and thread milling. See also "Ramping" and "Thread Milling".
Helix Angle
The helix angle is a characteristic of an endmill that is the angle from the vertical of the helical flutes. The most common helix angle is 30 degrees because it offers the broadest range of usability. Increased machine rigidity and solid carbide endmills argue that a 45 degree helix angle may be a better choice. The greater the angle, the faster the helix.
High Speed Machining or HSM
Using smaller cutters at much faster spindle speeds and feed rates to make many lighter cuts that take the place of deeper slower cuts with larger cutters in conventional machining.
If the speed is high enough, and the chips are evacuated well enough due to the high speeds and perhaps an air jet, coolant may not be necessary or may even be detrimental as the chips carry away most of the heat. Higher feed rates really facilitate this.
The advantages of HSM include higher accuracy, faster cycle times, and more accurate parts. Cutting forces are diminished in HSM, which can even result in greater tool life. Positive rake tooling also reduces cutting forces, and is desirable for HSM.
HSM requires the ability for the CNC machine axes to accelerate, decelerate, and move very quickly in order to make up for the time lost in making much lighter cuts.
The easiest way for the Home Shop Machinist to embrace high speed machining is often to attach a small high speed spindle such as a die grinder or laminate router to their existing mill head. Such spindles are self-contained with motor and run at speeds of 20,000 rpm and up. With a 1/8" or smaller endmill, they are well into the realm of HSM, especially for aluminum.
High Speed Steel or HSS
High Speed Steel, abbreviated HSS, refers to steel used to make cutters. It is called "high speed" because it is an alloy designed to withstand the heat of cutting better than milder steels. In the pantheon of cutter materials, HSS is one of the more common and plebian varieties. Carbide (See Also Carbide) is harder, more rigid, and withstands higher temperatures, although it is also more costly and more brittle on the downside.
Horizontal Machining Center
A machining center (See Also Machining Center) whose spindle is horizontal. Roughly analogous to a very sophisticated horizontal mill.
I
IGES
Initial Graphics Exchange Specification. It is a common file format for exchanging CAD data. PCBWay can use IGES solid or surface files to create molded parts.
Index Pulse
A pulse usually associated with spindle indexing that determines when a point on a rotating shaft has been passed. See also Spindle Indexing.
Indexable Tooling
Indexable tooling uses carbide inserts (See Also Carbide Insert) as the cutting edges. When the insert dulls or chips, it can easily be replaced with a new one for a fraction of the cost of replacing the whole tool.
Injection
The act of forcing molten resin into the mold to form the part.
Insert
An easily changeable cutting surface that may be used with indexable tooling (See Also Indexable Tooling). Inserts are generally very cheap compared to the cost of replacing the entire cutting tool, and so provide an economical way to use carbide (See Also Carbide or Carbide Insert) for high performance cutting in machine tools.
Inserts can be carbide, diamond, ceramic, or various other materials.
Insert Drill
A type of indexable tooling that uses a carbide insert to bore a hole. Each drill is designed for a specific size hole. Often, insert drills will have coolant passages to allow coolant to be pumped through the drill and down to the very bottom of the hole.
J
Jetting
Flow marks caused by the resin entering a mold at high speed, typically occurring near a gate.
Jig
Generically jigs and fixtures are used to guide and hold the workpiece. A jig may also guide the tool, while a fixture does not.
Jog, Jogging, and Jog Mode
Jogging is the operation of manually causing an axis to move under power. It is often convenient to jog using a handheld pendant control (See Also Pendant). A mechanism is usually provided to control the speed of jogging.
K
Knit lines
Also known as “stitch lines” or “weld lines,” and when multiple gates are present, “meld lines.” These are imperfections in the part where separated flows of cooling material meet and rejoin, often resulting in incomplete bonds and/or a visible line.
Keyboard Emulator
A keyboard emulator is an electronic circuit that accepts a number of inputs and converts them to keystrokes which are fed into the PC’s keyboard input. This is a convenient way to add additional control panel inputs on systems that use a parallel breakout board (See Also Breakout Board) because it conserves scarce input lines on the parallel port. IPAC is one example of a keyboard emulator board.
Knee Mill
Knee mills support the table, X, and Y axes on a knee and raise the table up and down whereas a bed mill (See Also Bed Mill) moves the spindle up and down. The Bridgeport manual mills were classic knee mills, but most modern CNC vertical machining centers are bed mills.
L
Layer thickness
Also known as “stitch lines” or “weld lines,” and when multiple gates are present, “meld lines.” These are imperfections in the part where separated flows of cooling material meet and rejoin, often resulting in incomplete bonds and/or a visible line.
LIM
Liquid injection molding, which is the process used in the molding of liquid silicone rubber.
Live tooling
Mill-like machining actions in a lathe where a rotating tool removes material from stock. This allows for the creation of features like flats, grooves, slots, and axial or radial holes to be created within the lathe.
Living hinge
Very thin section of plastic used to connect two parts and keep them together while allowing them to open and close. They require careful design and gate placement. A typical application would be the top and bottom of a box.
Ladder Diagram
A ladder diagram is an electrical schematic drawn according to a convention that has the two ladder "rails" being power supply lines and the "rungs" of the ladder between circuitry that passes between the two lines. The left line is normally hot and the right line is ground. The practice is used extensively for machine control systems and is useful because for troubleshooting one simply checks out each "rung" until the problem is found. A circuit drawn in this way is sometimes referred to as "Ladder Logic" or "Relay Logic".
Lapping
Lapping is a process of rubbing two mating surfaces together with an abrasive grit in between to ensure they fit smoothly and closely together. Lapping does not necessarily ensure flatness, in fact it may achieve just the opposite effect unless carefully applied.
Laser Interferometry
Laser interferometry is a very high precision method of measurement that is commonly used to align commercial CNC tools.
Lead
The axial distane the nut advances in one revolution of the leadscrew. The lead is equal to the pitch times the number of screw starts. See Also Screw Starts.
Lead Angle
Lead Angle refers to the angle of engagement for cutters, usually milling cutters such as face mills. A 90 degree face mill cuts a square shoulder, while a 45 degree facemill leaves an angled shoulder. The more angle from the vertical, the greater the lead angle. Why use a higher lead angle? Because it allows a higher feedrate. A 45 degree facemill can be fed at 1.4 times the feedrate of the 90 degree facemill and will generally deliver a better surface finish while doing so. This is because of the relative chip thickness or chipload of one cutter versus the other:
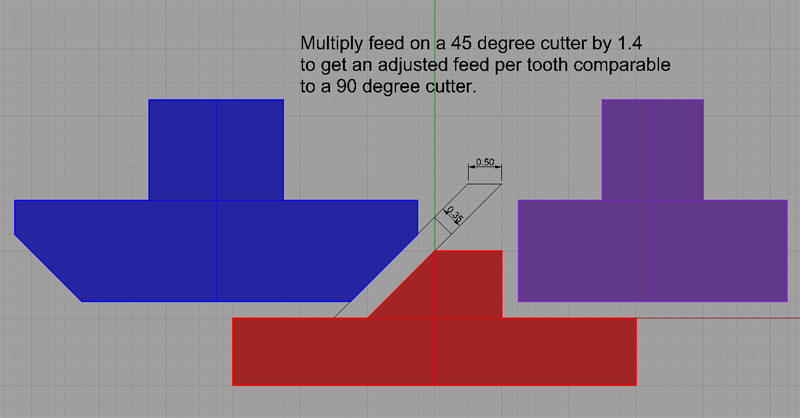
Notice that when fed 0.5" the actual chip thickness of the 45 degree cutter is only 0.35", hence the higher feedrates...
Leadscrew
A generic device for translating rotary to linear motion. There are many different kinds of leadscrews including ACME and ballscrews (See Also ACME and Ballscrew).
Linear Motion
Motion in a straight line and all those components and technologies associated with that motion.
Linear Scale
A linear scale is an electronic device used to measure a position along a line. Linear scales are commonly used in DRO’s (See Also DRO) and sometimes to provide feedback information in sophisticated closed loop systems (See Also Closed Loop).
Linear Ways
Sliding ways are used by many machine tools so that their axes may slide against one another. There are four prominent designs:
- Dovetail Ways: Very common on mills, dovetail ways look like the dovetails used in wood joinery.
- Box Ways: Box Ways are rectangular cross section, as opposed to the angular shape of dovetail ways. Box ways are very strong, but they suffer from two shortcomings. First, they involve a lot of surface contact area, so managing friction is key. Second, in order to slide at all, some clearance is required, which results in some slop in their travel. They are the strongest and most rigid design, but they are difficult and expensive to manufacture.
- Prismatic Ways: These are prism shaped ways common to lathes.
- Linear Ways: Linear ways use linear slides as rails and so are much different than the other three styles. The roll on ball bearings as opposed to having more metal-to-metal contact in the other designs. Linear ways will have the least rigidity, but for the price, they are ideal for precision and high speeds.
Load Meter
Load meters are common on CNC machines. They give the operator one way to gauge how hard the machine is working, which is something that's harder to do on CNC where there is no manual "touch". Usually load meters are just ammeters that measure the amount of current the spindle motor is drawing. Some machines also offer load meters on the individual axes, for example to measure how hard it is to feed.
Load meters have a lot of interesting uses. For example, during roughing, the load meter can be used to tell when feeds and speeds and DOC are aggressive enough to be near the machine's capacity. Another use is to observe the load meter while drilling a hole. If the load increases the deeper into the hole the machine gets, it is an indication that chips are not being evacuated well enough. It may be time to fool with the coolant delivery or look at other steps to improve chip evacuation.
M
Medical grade
Resin that may be suitable for use in certain medical applications.
Meld lines
Occurs when multiple gates are present. These are imperfections in the part where separated flows of cooling material meet and rejoin, often resulting in incomplete bonds and/or a visible line.
Metal safe
A change to the part design that requires only the removal of metal from the mold to produce the desired geometry. Typically most important when a part design is changed after the mold has been manufactured, because then the mold can be modified rather than entirely re-machined. It is also commonly called “steel safe.”
Mold release spray
A liquid applied to the mold as a spray to facilitate the ejection of parts from the B-side. It is typically used when the parts are difficult to eject because they are sticking to the mold.
Multi-cavity mold
A mold where more than one cavity is cut into the mold to allow for multiple parts to be formed in one cycle. Typically, if a mold is called “multi-cavity,” the cavities are all the same part number. See also “family mold.”
Mach 3
Mach 3 is a very popular CNC Controller that runs on a PC under Windows and is sold by Artsoft.
Machine Coordinates
The absolute coordinates or position of the axes. Machine coordinates are always 0 or positive.
Machine Zero
Movement along an axis in the farthest possible positive direction. It is synonymous with the Home Position of the machine. Many machines will have Home Switches at this location so that the axes can be commanded to move until the Home Switches are triggered, telling the machine it is exactly at Machine Zero. See Also Home Switches. Other common names for Machine Zero are Machine Reference and Reference Point.
Machining Center
A CNC tool that can perform multiple operations in the same setup with automatic tool change.
N
Net shape
The final desired shape of a part; or a shape that does not require additional shaping operations before use.
Nozzle
The tapered fitting on the end of the barrel of the injection-molding press where the resin enters the sprue.
Negative Rake
Rake is the angle from the workpiece wall to the cutting tool at the cutting edge. If it is 90 degrees, the edge is perpendicular to the workpiece. Angles less than 90 degrees are negative rake angles. Angles greater than 90 degrees are positive rake angles. Positive rake is generally preferable to negative rake because it requires less pressure to cut. Negative rake has the advantage that it provides more edges on a carbide insert (See Also Carbide Insert) that may be used, and may be more economical.
NEMA (23, 34, 42, Enclosure)
NEMA is the National Electronic Manufacturers Association. It is a standard setting group. The relevant standards for CNC purposes include NEMA enclosures, which make suitable enclosures for CNC electronics and the standards for motor mounting, which are what NEMA 23, NEMA 34, and NEMA 42 are.
Normalizing
Normalizing is a process used to relieve internal stress in a material. There are a variety of procedures used that are dependent on the material. If you machine material that has not been normalized, internal stress may cause that material to warp during or shortly after the machining process. There are methods used to deal with this, but normalizing the material takes care of the problem right up front.
O
On-axis hole
This is a hole that is concentric to the axis of revolution of the turned part. It is simply a hole on the end of a part and in the center.
Overflow
A mass of material away from the part, typically at the end of fill, connected by a thin cross-section. The overflow is added to improve part quality and is removed as a secondary operation.
Offsets
A pre-determined distance entered into and used by the CNC controller.
Oldham Coupler
An Oldham coupler is a type of shaft coupler that incorporates slots sandwiching a middle piece to allow misalignment of the shafts without backlash, similar to a helical beam coupler (See Also Helical Beam Coupler).
Oz – in
A measurement of torque. See also “Torque”.
P
Packing
The practice of using increased pressure when injecting a part to force more plastic into the mold. This is often used to combat sink or fill problems, but also increases the likelihood of flash and may cause the part to stick in to the mold.
Parasolid
A file format for exchanging CAD data.
Part A/Part B
LSR is a two-part compound; these components are kept separate until the LSR molding process begins.
Parting line
The edge of a part where the mold separates.
Pickouts
A mold insert that remains stuck to the ejected part and has to be pulled out of the part and placed back into the mold before the next cycle.
PolyJet
PolyJet is a 3D printing process where small droplets of liquid photopolymer are sprayed from multiple jets onto a build platform and cured in layers that form elastomeric parts.
Porosity
Undesired voids included in a part. Porosity can manifest in many sizes and shapes from many causes. Generally, a porous part will be less strong than a fully dense part.
Post gate
A specialized gate that uses a hole that an ejector pin passes through to inject resin into the mold cavity. This leaves a post vestige that usually needs to be trimmed.
Press
An injection molding machine.
Parametric Drawing
Parametric drawing refers to a feature of CAD programs that allows the dimensions of the parts to act as parameters. One can change a dimension and the part will adjust its size accordingly. This is very convenient for revising drawings. The feature does not exist in all CAD programs. SolidWorks and Alibre 3D have it, while Rhino 3D does not.
Peripheral Milling
Any milling that uses the edge of the milling cutter that is parallel to the axis of rotation instead of the end of the cutter, as in Face Milling (See Also Face Milling).
PID
PID is a type of servo or feedback tuning system which stands for Proportional, Integral, and Derivative.
Pinch Turning (Also Called “Balanced Turning”)
Like Follow Turning, Pinch Turning is a way to employ 2 independent tool turrets on a CNC lathe to cut more quickly. When pinch turning one tool follows behind the other. The first tool cuts a spiral swatch (not unlike threading) and the second tool cleans up the spiral of uncut material left by the first tool.
Pitch or Leadscrew Pitch
Usually, the number of turns the leadscrew must make to travel a standard distance. For Imperial screws, the standard distance will be an inch and the unit of measure would be TPI or Turns Per Inch. A more accurate and technical definition is the axial distance between threads, which will be equal to the lead in a single start screw. See Also Lead and Screw Starts.
Plasma Table
A gantry style (See Also Gantry) machine used to move a plasma cutting torch over sheets of metal under CNC control.
Plunge
To cut straight down, similar to drilling with a twist bit.
Pocket
An interior recess that is cut into a part.
Positive Rake
Rake is the angle from the workpiece wall to the cutting tool at the cutting edge. If it is 90 degrees, the edge is perpendicular to the workpiece. Angles less than 90 degrees are negative rake angles. Angles greater than 90 degrees are positive rake angles. Positive rake is generally preferable to negative rake because it requires less pressure to cut. Negative rake has the advantage that it provides more edges on a carbide insert (See Also Carbide Insert) that may be used, and may be more economical.
Preload (Bearings and Leadscrews)
Preload is a mechanism used to eliminate backlash by tensioning a bearing or leadscrew to take up the slack that causes backlash.
Some typically ways in which preload can be achieved include using a threaded screw that is torqued down to create a load, using spacers or shims, using springs, wavy (Belleville) washers, or using oversized balls in a ballnut.
Q
Quill
The Quill is a spindle feature whereby just the spindle cartridge may be raised and lowered using a rack and pinion without moving the whole head. It is common on manual milling machines and drill presses, but is usually omitted from CNC milling machines.
R
Radial hole
This is a hole formed by live tooling that is perpendicular to the axis of revolution of a turned part, and could be considered a side hole. The center line of these holes are not required to intersect the axis of revolution.
Radiused
An edge or vertex that has been rounded. Typically, this occurs on part geometries as a natural result of the PCBWay' milling process. When a radius is intentionally added to an edge on a part, it is referred to as a fillet.
Ram
A hydraulic mechanism that pushes the screw forward in the barrel and forces resin into the mold.
Recess
An indentation in the plastic part caused by the impact of the ejector pins.
Reinforced resin
Refers to base resins with fillers added for strength. They are particularly susceptible to warp because the fiber orientation tends to follow flow lines, resulting in asymmetric stresses. These resins are typically harder and stronger but also more brittle (e.g., less tough).
Resin
A generic name for chemical compounds that, when injected, form a plastic part. Sometimes just called “plastic.”
Resolution
The level of printed detail achieved on parts built through additive manufacturing. Processes like stereolithography and direct metal laser sintering allow for extremely fine resolutions with the smallest of features.
Rib
A thin, wall-like feature parallel to the mold opening direction, common on plastic parts and used to add support to walls or bosses.
Runner
A channel that resin passes through from the sprue to the gate/s. Typically, runners are parallel to, and contained within, the parting surfaces of the mold.
Recutting
Recutting occurs when chips are not evacuated quickly enough to avoid the cutting tool hit them again after they’ve already been cut. This forces the chip against the cut again, which is bad for surface finish and tool wear.
One strategy to reduce recutting is to use climb instead of conventional milling.
Refractometer
A refractometer is an optical device used to measure the index of refraction of a material. In CNC use, refractometers are used to measure whether coolants, which are made from concentrate, are mixed in the correct ratios. Failure to mix a coolant properly can lead to sub-standard performance as well as a greater likelihood the coolant may go rancid.
Relative Coordinates & Positioning
Relative Coordinates, also called Incremental Coordinates, refers to the system by which the part program determines how to move. Absolute coordinates are expressed relative to a fixed position whereas Relative Coordinates (see also) are relative to the current position of the cutting tool. The G90 command places the part program into absolute coordinate mode. G91 cancels absolute coordinate mode and places the part program into relative coordinate mode.
Relative Zero
Relative Zero is the name of the origin of the Relative Coordinate system, in other words, it is the current location of the tool. See Also Relative Coordinates.
Repeatability
Repeatability for a CNC machine is the ability to reach the same level of accuracy over and over again.
Resolution
How accurately a CNC machine or component can discern position. Encoders have a resolution as do digital calipers and other devices. Clearly, it is hard for accuracy (See Also Accuracy and Repeatability) to exceed resolution. Typically accuracy is much less than resolution, in fact.
Resolver
Resolvers are rotary transformers that produce a signal proportional to the rotor position. They are used on older machines before optical encoders became readily available. Generally, they only work with older controls systems and are often replaced with optical encoders (See Also Encoder) when the machine is refitted with a new control.
Rhino 3D
Rhino 3D is a CAD program that may be used to generate solid models.
Right-Hand Rule
The right-hand rule is a convenient way to know the location of the X-, Y-, and Z- axes as well as which direction is positive. Simply hold out your right hand with the thumb, index finger, and second finger at right angles to one another. Point your thumb to the right (X-Axis), the index finger straight ahead (Y-Axis), and the second finger straight up (Z-Axis). Note that this only works for axes as defined for mills (See Also Axes):
Rigid Tapping
Rigid tapping is a CNC capability where a tap is placed in a tool holder and the machine spins the tap while lowering it at exactly the correct speed to cut threads. It is called rigid because an alternate method, called floating tapping, allows the tap to float relative to the spindle so that the threading process pulls the tap along at the right speed. Rigid tapping requires precise synchronization of spindle speed with Z-axis motion much like tapping on a lathe.
Roughing
Roughing means to machine a lot of material without concern for surface finish.
Round Column Mill
A round column mill is similar to a drill press. It uses a round column to support the spindle. Z-axis moves are made using a quill (see also Quill) because the spindle cannot be moved along the column without losing x and y position. This makes these mills less desireable for CNC applications, because the entire machining operation must be completed without moving the Z-axis except via quill, which has very limited travel.
S
Scraping
Scraping is the preferred method of ensuring flatness with a very high degree of precision. It is a manual task and a somewhat difficult task to learn. The “bible” for information on scraping is a book called Machine Tool Reconditioning by Connelly.
Screw
A device in the barrel that compacts resin pellets to pressurize and melt them prior to injection.
Screw Machine
Any lathe that creates parts from continuously fed bar stock. Swiss Lathes are a particular type of screw machine, also called a Swiss-style Screw Machine. See Also Swiss Lathe. Some authorities require a screw machine to have multiple spindles, but definitions vary.
Selective laser sintering (SLS)
During the SLS process, a CO2 laser draws onto a hot bed of thermoplastic powder, where it lightly sinters (fuses) the powder into a solid. After each layer, a roller lays a fresh layer of powder on top of the bed and the process repeats.
Shear
The force between layers of resin as they slide against each other or the surface of the mold. The resulting friction causes some heating of the resin.
Short shot
A part that wasn't completely filled with resin, causing short or missing features.
Shrink
The change in part size as it cools during the molding process. This is anticipated based on material manufacturer recommendations and built into the mold design before manufacturing.
Shutoff
A feature that forms an internal through-hole in a part by bringing the A-side and B-side in contact, preventing the flow of resin into the through-hole.
Slideways
Sliding ways are used by many machine tools so that their axes may slide against one another. There are four prominent designs:
- Dovetail Ways: Very common on mills, dovetail ways look like the dovetails used in wood joinery.
- Box Ways: Box Ways are rectangular cross section, as opposed to the angular shape of dovetail ways. Box ways are very strong, but they suffer from two shortcomings. First, they involve a lot of surface contact area, so managing friction is key. Second, in order to slide at all, some clearance is required, which results in some slop in their travel. They are the strongest and most rigid design, but they are difficult and expensive to manufacture.
- Prismatic Ways : These are prism shaped ways common to lathes.
- Linear Ways : Linear ways use linear slides as rails and so are much different than the other three styles. The roll on ball bearings as opposed to having more metal-to-metal contact in the other designs. Linear ways will have the least rigidity, but for the price, they are ideal for precision and high speeds.

Box Ways vs Dovetail Ways...
Slot Milling
Milling a channel in the surface of a workpiece. For best accuracy and surface finish, a cutter narrower than the slot width can be used. Cut the middle of the slot first, and then cut each edge so that the final finish does not require the cutter to machine on both sides at once.
Solidworks
Solidworks is an extremely popular CAD program often used for CNC applications. Some say it is the most popular software used by CNC professionals.
Sturz Milling
A technique used in 5-axis milling where a ballnose cutter is operated at an angle other than vertical to the surface to that the dead spot on the end of the endmill that's hardly moving is not used. If you look at a ballnose cutter, the effective cutting speed reduces the closer you get to the tip until it is theoretically zero right on the tip. It is possible to utilize Sturz milling without a 5-axis machine so long as the orientation of the workpiece is such that the dead tip of the cutter is not engaged in the workpiece..
Swiss Lathe
A lathe whereby the work is fed through the spindle to provide Z-axis motion--the tooling does not move in Z. Most lathes keep the workpiece fixed and only the tool moves in relation to the rotating workpiece. Swiss lathes excel at creating complex small cylindrical parts. Swiss lathes may also have multiple spindles. They are a type of screw machine.
Side-action
A portion of the mold that is pushed into place as the mold closes, using a cam-actuated slide. Typically, side-actions are used to resolve an undercut, or sometimes to allow an undrafted outside wall. As the mold opens, the side action pulls away from the part, allowing the part to be ejected. Also called a “cam.”
Sink
Dimples or other distortion in the surface of the part as different areas of the part cool at different rates. These are most commonly caused by excessive material thickness.
Splay
Discolored, visible streaks in the part, typically caused by moisture in the resin.
Sprue
The first stage in the resin distribution system, where the resin enters the mold. The sprue is perpendicular to the parting faces of the mold and brings resin to the runners, which are typically in the parting surfaces of the mold.
Steel pins
A cylindrical pin for formatting high-aspect-ratio, small-diameter holes in a part. A steel pin is strong enough to handle the stress of ejection and its surface is smooth enough to release cleanly from the part without draft.
Steel safe
Also known as “metal safe” (the preferred term when working with aluminum molds). This refers to a change to the part design that requires only the removal of metal from the mold to produce the desired geometry. Typically most important when a part design is changed after the mold has been manufactured, because then the mold can be modified rather than entirely re-machined.
STEP
Stands for Standard for the Exchange of Product Model Data. It is a common format for exchanging CAD data.
Stereolithography (SL)
SL uses an ultraviolet laser focused to a small point to draw on the surface of a liquid thermoset resin. Where it draws, the liquid turns to solid. This is repeated in thin, two-dimensional cross-sections that are layered to form complex three-dimensional parts.
Sticking
A problem during the ejection phase of molding, where a part becomes lodged in one or the other half of the mold, making removal difficult. This is a common issue when the part is not designed with sufficient draft.
Stitch lines
Also known as “weld lines” or “knit lines,” and when multiple gates are present, “meld lines.” These are imperfections in the part where separated flows of cooling material meet and rejoin, often resulting in incomplete bonds and/or a visible line.
STL
Originally stood for “STereoLithography.” It is a common format for transmitting CAD data to rapid prototyping machines and is not suitable for injection molding.
Straight-pull mold
A mold that uses only two halves to form a cavity that resin is injected into. Generally, this term refers to molds with no side-actions or other special features used to resolve undercuts.
T
Tab gate
An opening aligned with the parting line of the mold where resin flows into the cavity. These are also referred to as “edge-gates” and are typically placed on an outside edge of the part.
Tear Strip
A feature added to the mold that will be removed from the part after molding to aid in creating a crisp end on the part. This is often done in conjunction with an overflow to improve the final part quality.
Tempered
Tempering is a heat treating process that is used to reduce the hardness of a material to a defined level. Often it may not be desirable to use the full hardness possible with the allow, perhaps because it will be too brittle or too hard to work. Tempering goes back after the initial hardening treatment and raises the material to a particular temperature associated with the desired hardness.
Texture
A specific type of surface treatment applied to some or all faces of the part. This treatment can range from a smooth, polished finish to a highly contoured pattern that can obscure surface imperfections and create a better looking or better feeling part.
Thread Milling
Thread milling is a method for producing a thread on a milling machine. To cut a thread using a mill, helical interpolation (see also "Helical Interpolation") is used to describe the helical motion of the threads. A single point cutter is used to cut one or more threads.
Tunnel gate
A gate that is cut through the body of one side of the mold to create a gate that does not leave a mark on the exterior face of the part.
Turning
During the turning process, rod stock is rotated in a lathe machine while a tool is held against the stock to remove material and create a cylindrical part.
U
Undercut
A portion of the part that shadows another portion of the part, creating an interlock between the part and one or both of the mold halves. An example is a hole perpendicular to the mold opening direction bored into the side of a part. An undercut prevents the part from being ejected, or the mold from opening, or both.
V
Vent
A very small (0.001 in. to 0.005 in.) opening in the mold cavity, typically at the shutoff surface or via an ejector pin tunnel, that is used to let air escape from a mold while the resin is injected.
Vertical Machining Center
A Machining Center (See Also Machining Center) intended for mlling operations whose spindle is vertical. Think of them as very sophisticated CNC milling machines.
Vestige
After molding, the plastic runner system (or in the case of a hot tip gate, a small dimple of plastic) will remain connected to the part at the location of the gate/s. After the runner is trimmed off (or the hot tip dimple is trimmed), a small imperfection called a “vestige” remains on the part.
Vertical Turning Center
A Machining Center (See Also Machining Center) intended for turning operations whose spindle is vertical. Think of them as very sophisticated CNC lathes.
W
Wall
A common term for the faces of a hollow part. Consistency in wall thickness is important.
Warp
The curving or bending of a part as it cools that results from stresses as different portions of the part cool and shrink at different rates. Parts made using filled resins may also warp due to the way the fillers align during resin flow. Fillers often shrink at different rates than the matrix resin, and aligned fibers can introduce anisotropic stresses.
Weld lines
Also known as “stitch lines” or “knit lines,” and when multiple gates are present, “meld lines.” These are imperfections in the part where separated flows of cooling material meet and rejoin, often resulting in incomplete bonds and/or a visible line.
Wireframe
A type of CAD model consisting only of lines and curves, in 2D or 3D. Wirefame models are not suitable for rapid injection molding.